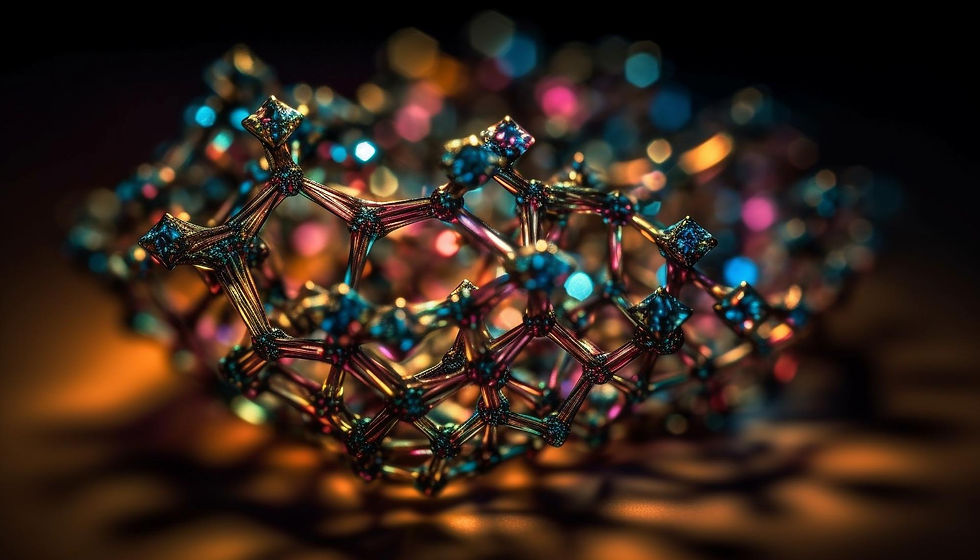

Patentierte Vernetzersysteme für Pulverlacke - effizient, wirtschaftlich und umweltfreundlich.
Das Chemieunternehmen CICONIAS ist spezialisiert auf die Herstellung von Vernetzer-/Härtersystemen für Pulverlacke auf Basis einer eigenen, patentierten Polynitronentechnologie. 2020 konnte das Unternehmen nach langwierigen und intensiven Tests das Produkt unter der Handelsbezeichnung OLIGONAT vorstellen.
Ohne signifikante Änderungen am bestehenden Produktionsprozess ermöglicht OLIGONAT drastische Energieeinsparungen im Härtungsprozess von Pulverlacken von mehr als 30% durch die Reduzierung der dafür notwendigen Einbrenntemperaturen. Dies hat starke positive Auswirkungen auf die Wirtschaftlichkeit der Pulverlackproduktion indem die Energiekosten gesenkt werden. Gleichzeitig wird dadurch auch der ökologische Fußabdruck der Pulverlackproduktion deutlich reduziert, was Compliance mit regulatorischen Umweltauflagen erhöht. Weiterhin ermöglicht die reduzierte Einbrenntemperatur die Beschichtung von temperatursensiblen Materialien wie z.B. MDF, was die mögliche Produktpalette der Hersteller erweitert.

TRENDS SIND FLÜCHTIG, INNOVATION BLEIBT
Durch den industriellen Einsatz und die weitaus geringere Vernetzungstemperatur wird schon während des Beschichtungsprozesses erheblich CO2 eingespart. Oligonat enthält keinerlei Lösungsmittel und unterliegt den aktuellen VOC-Richtlinien (Volatile Organic Components). Die kostenintensive und umweltschädliche Entsorgung von Altgebinden und Härter entfällt vollständig.
Zurzeit gibt es keine vergleichbaren Lösungen im Hinblick auf die Umweltfreundlichkeit und den technologischen Fortschritt, den unsere Additive als essenzielle Vernetzer bieten. Dies begründet das Alleinstellungsmerkmal von Oligonat. Weiterhin ist Oligonat auch für die Herstellung von Polymeren auf anderen Anwendungsgebieten wie zum Beispiel dem Bereich der Haft- und Klebstoffe sehr gut geeignet. Spezielle Applikationen können wir jederzeit kundenspezifisch entwickeln und anbieten.

VORTEILE AUF EINEN BLICK
ANWENDUNGS-
BEREICHE
Umweltfreundlich
Pulverlacke sind frei von Lösungsmitteln, unterliegen den VOC-Richtlinien und die Entsorgung von Altgebinden und Härter entfällt
Kostengünstig
Der Materialverbrauch ist minimal und die Kosten für die Entsorgung von Reststoffen entfallen
Qualität
Pulverlacke sind widerstandfähiger und langlebiger (UV-Schutz, Korrosionsschutz, abriebfest, chemiekalienbeständig)
Wirtschaftlich
Pulverlackbeschichtung läuft weitgehend automatisch ab. Das Endergebnis ist ein gleichmäßigeres Finish da das Pulver auf einmal über das gesamte Objekt schmilzt und keine Anwendungsspuren oder Tropfen hinterlässt
Vielseitig
Die Pulverbeschichtung bietet ein breites Farbkartenspektrum: Sonderfarben und unterschiedliche Glanzgrade können einfach realisiert werden. Durch innovative Effektpulverlacke stellen Glanzglimmer- und Metallikeffekte kein Problem dar
Dynamisch
Die Pulverbeschichtung bleibt dynamisch und weist weitaus seltener Risse auf
Schutzbeschichtungen
Korrosions-, UV- und Witterungsschutz
Architektur
Fassadenveredlung, feuerhemmend bei Holzfassaden und Dächern. Beispiele: Bird-Nest Olympic Stadium Beijing, Swatch Headquarter Biel
Automobillackierung
Karosserie, Felgen, Interieur
Landwirtschaft
Traktoren, Mähdrescher, Anhänger etc.
Pipelines
Gas-, Öl-, und Wasserindustrie
Energie
z.B. Kraftwerke und Kraftwerkbauteile
Haushaltsgeräte
z.B. Öfen, Mikrowellen, Spülmaschinen, Kühlschränke
Möbellackierung
z.B. Massivholz, Spanplatten, Melamin, grundierte Platten, Sperrholz und Furniere
Telekommunikation
z.B. Computer, Home-Entertainment, Spielekonsolen Handys

Geschichte des Pulverlacks - über 60 Jahre Innovation
1961:
Erste Beschichtungsverfahren werden für Metallteile, Aluminium und Kunststoff entwickelt und angewendet.
1964:
Erste Lackierkabinen werden zu Beschichtungskabinen umgebaut.
1968:
Entwicklung der Hybridpulverlacke (Epoxid und Polyester als Bindemittel). Dadurch werden kürzere Aushärtezeiten und eine konstantere Qualität erreicht.
1972:
Entwicklung der heute gebräuchlichen Korona-Pistole, welche die Zuführung von Hochspannung innerhalb der Lackierpistole ermöglicht. Zusätzlich wurden erste Pulverlacke entwickelt, welche die dort verwendete Aufladung durch Reibung in vollem Umfang nutzen.
1976:
Vorstellung von Beschichtungskabinen mit Bandfilter, die Farbwechselzeiten von unter 20 Minuten ermöglichten.
1980:
Beschichtungskabinen werden aus Kunststoff hergestellt und mit runden Ecken ausgestattet, um die Reinigung durch erschwerte Anhaftung von Pulverpartikeln zu vereinfachen.
1985:
Die Flachstrahldüse, die heute bei 80% der Pulverbeschichtungsanlagen im Einsatz ist, wird erfunden.
1990:
Pulverlackfördergeräte werden angeboten, welche die Förderung direkt aus Gebinden ermöglichen. Diese Technologie befindet sich heute in breitem Einsatz.
1995:
Pulverlacke werden erstmalig in der Automobilindustrie eingesetzt.
2000:
Einführung von Harzen mit niedrigeren Vernetzungstemperaturen ermöglichen die Beschichtung von Holz und anderen hitzeempfindlichen Materialen.
2001:
Einführung der VOC-Richtlinien (Verordnung zur Umsetzung der Richtlinie 1999/13/EG über die Begrenzung von Emissionen flüchtiger organischer Verbindungen).
2007:
Erstmals wurden mehr als 70.000t Pulverlack in Deutschland produziert.
2020:
Die Cinartis GmbH patentiert Oligonat, wodurch der gesamte Prozess nachhaltiger und umweltschonender wird.